Steel Belt Granulator—A High-Quality Choice for Efficient Granulation Technology
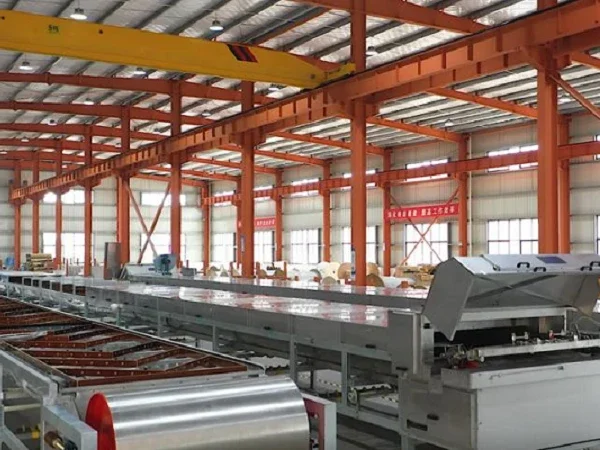
The steel belt granulator is a type of efficient granulation equipment widely used in the chemical, pharmaceutical, food, metallurgical, and other industries. With its unique design and advanced cooling technology, the steel belt granulator can perform stable and efficient granulation operations in complex environments. The equipment quickly solidifies high-temperature molten materials into uniform particles through high-speed cooling and precise spraying, meeting the needs of various industrial productions. This article Little SKy will explore the working principle and structural composition of the steel belt granulator, and provide a deep understanding of its important role in modern industrial production.
The Working Principle of Steel Belt Granulator
The core working principle of the steel belt granulator is to use a cooling steel belt and a cooling system to quickly cool down and solidify molten materials into particles. This process mainly includes four stages: heating, spraying, cooling, and collection. The efficient operation and close cooperation of each step ensure the stability of the granulation effect and uniformity of products.
Heating of Molten Materials
The operation of the steel belt granulator begins with heating the material to a molten state. Different materials have different melting points. The heating system of the steel belt granulator typically uses electric heating or steam heating to enable the material to reach a liquid state quickly for easy spraying and distribution. During this process, temperature control is extremely important; too high a temperature may cause the material to decompose, while insufficient temperature will lead to poor fluidity and affect the uniformity of the particles.
Spraying Evenly on the Cooling Steel Belt
The molten material is sprayed onto the cooling steel belt through a high-precision nozzle. The design of the spraying system directly affects the size, shape, and uniformity of the particles. The high-precision nozzle can control the flow rate and distribution of the spraying to ensure that the material is evenly distributed on the steel belt, thereby forming particles of uniform size and regular shape. The precise spraying system also reduces material waste and agglomeration, improving granulation efficiency.
Rapid Cooling of the Cooling Steel Belt
The cooling steel belt is a key component of the steel belt granulator, made of a special metal material with strong thermal conductivity. The cooling steel belt is connected to a water cooling or air cooling system to quickly cool the high-temperature material to a solid state, forming particles. This cooling method is not only efficient but also stable, avoiding the adhesion and agglomeration problems between particles and ensuring high quality.
Particle Collection
The solidified particles are conveyed to the collection device by the steel belt. The collection device automatically screens, packages, and conveys the particles to the next production link. Through reasonable temperature and speed control, the entire granulation process can be carried out smoothly, ensuring that the specifications of the particles meet production requirements.
This working principle of the steel belt granulator improves granulation speed and ensures the quality of the particles, making it an important player in modern industrial production.
Main Structure of the Steel Belt Granulator
The scientific structural design is the reason why the steel belt granulator can be granulated efficiently. Generally speaking, the steel belt granulator consists of a melting system, a spraying system, a cooling steel belt, a cooling system, and a collection device. The precise combination and good cooperation of these components enable the steel belt granulator to have excellent working performance and high stability.
Melting System
The melting system is responsible for heating the material to a suitable melting temperature for spraying and flow. Most steel belt granulators use electric heating or steam heating for melting systems, achieving precise temperature control to meet the melting requirements of different materials. The melting system is usually equipped with a temperature control sensor that can monitor temperature changes in real time, ensuring that the material is always in the best melting state, thus providing a guarantee for subsequent spraying and cooling.
Spraying System
The primary function of the spraying system is to evenly distribute the molten material onto the cooling steel belt. Its core component is a high-precision nozzle. The precision of the nozzle determines the spraying speed and distribution range of the material, which directly affects the size and shape of the particles. High-precision nozzles can also reduce material waste and adhesion, ensuring that the particles are of uniform size and regular shape. The spraying system will be adjusted according to the properties of the material during design to accommodate materials with different fluidity and viscosity.
Cooling Steel Belt
The cooling steel belt is one of the core components of the steel belt granulator and is made of high-temperature and corrosion-resistant metal materials. During the high-speed rotation process, the cooling steel belt can quickly cool and solidify the molten material into particles. Its smooth surface has excellent thermal conductivity, ensuring the uniformity and integrity of the particles. The width and length of the cooling steel belt can be adjusted according to production needs to meet the specifications of particles of different sizes.
Cooling System
The cooling system of the steel belt granulator primarily has two types: water cooling and air cooling. By connecting with the cooling steel belt, the material can be quickly cooled. The water cooling system is typically used for high-temperature and high-viscosity materials with a fast cooling speed, while the air cooling system is suitable for cooling relatively low-temperature materials. The efficiency and stability of the cooling system play a decisive role in the granulation effect, and its design will also be optimized and adjusted according to specific material characteristics and production requirements.
Collecting Device
The cooled and solidified particles are transported to the collecting device via the conveyor belt for screening, classification, and packaging. The collecting device has an automatic screening function and can classify the particles according to their sizes to meet the requirements for products of different specifications. The collecting device is reasonably designed and easy to operate, effectively reducing manual intervention in the production process and improving the level of automation.
These structural components of the steel belt granulator cooperate with each other, providing high efficiency, good stability, and easy operation. It can meet the requirements of large-scale production and has become widely used granulation equipment in various industries.
The steel belt granulator plays an important role in modern industry with its efficient and stable granulation effect. With its unique cooling system, precise spraying system, and good adaptability, the steel belt granulator is widely used in chemical, pharmaceutical, food, metallurgical, and other industries. Whether it involves high-temperature and high-viscosity resins and waxes or pharmaceutical particles requiring high quality and uniformity, the steel belt granulator can provide efficient and high-quality granulation solutions.
https://www.th-littlesky.com/PRODUCT
www.th-littlesky.com
Little Sky Mechanical Engineering Thailand Co.,Ltd