Hydraulic cylinders lacking load capacity? Learn why and find the best fix
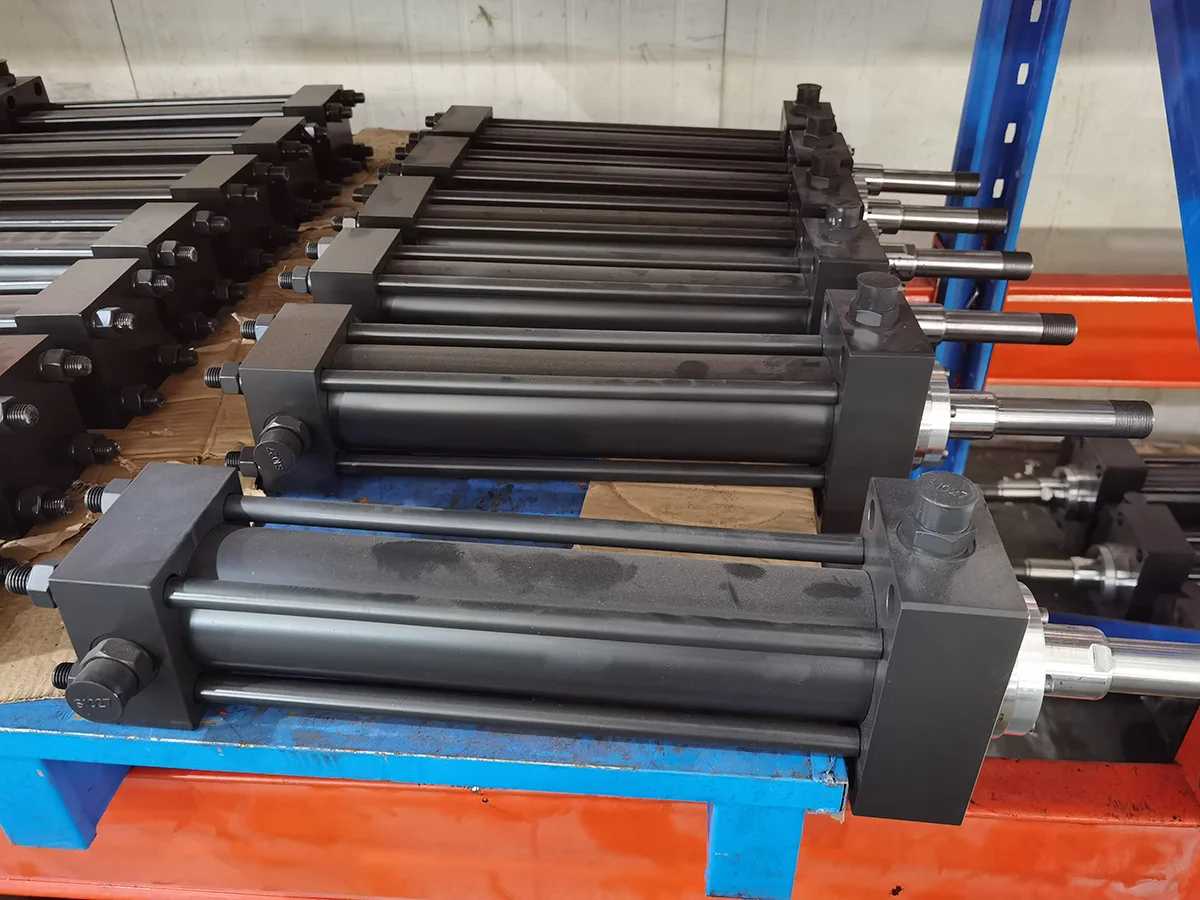
As the core actuator in the hydraulic system, the hydraulic cylinder is widely used in engineering machinery, mining equipment, aerospace, and other fields, bearing huge loads and complex work tasks. During long-term and high-load use, the load-bearing capacity of the hydraulic cylinder may gradually decrease, thus affecting the operating efficiency and safety of the overall system. Therefore, understanding the reasons for the decline in the load-bearing capacity of the hydraulic cylinder and taking effective solutions is of great significance for extending the service life and ensuring the stable operation of mechanical equipment.
1. Common reasons for the decline in the load-bearing capacity of the hydraulic cylinder
Overload: Overload is one of the most direct reasons for the decline in the load-bearing capacity of the hydraulic cylinder. In the hydraulic system, if the load borne by the hydraulic cylinder exceeds its designed load-bearing capacity, the performance of the hydraulic cylinder will drop sharply. This situation often occurs when the equipment fails, such as when the output pressure of the hydraulic pump is unstable or there is a problem with the adjustment system. Overload will not only cause direct damage to the hydraulic cylinder itself but also affect the stability of the entire hydraulic system.
Wear of internal parts of the hydraulic cylinder: Long-term use of the hydraulic cylinder will cause wear of its internal parts, such as pistons, piston rods, sealing rings, and other parts. The piston and piston rod are constantly moving under the action of hydraulic oil, which is prone to surface wear due to friction, and then leads to failure and leakage of the seal. Once the seal is not tight, the oil in the hydraulic cylinder cannot maintain sufficient pressure, resulting in a decrease in its load-bearing capacity. Especially under high pressure and high-speed working conditions, the wear of internal components will accelerate, greatly reducing the load-bearing capacity of the hydraulic cylinder.
Hydraulic oil contamination: The quality and cleanliness of the hydraulic oil directly affect the performance of the hydraulic cylinder. If the hydraulic oil contains impurities, metal particles, or moisture, it will have a great negative impact on the hydraulic system. Oil contamination will accelerate the wear of the internal components of the hydraulic cylinder, resulting in poor sealing and pressure drop. In addition, the presence of contaminants may also cause the hydraulic pump to work unstably, thereby affecting the load-bearing capacity of the hydraulic cylinder. When the hydraulic oil is seriously contaminated, the entire operating efficiency of the system will decrease.
Abnormal oil temperature: The working environment temperature of the hydraulic cylinder has a great influence on its load-bearing capacity. The viscosity of hydraulic oil at different temperatures is different. Too high or too low a temperature will affect the fluidity and lubricity of the oil. The high temperature will make the oil thinner, resulting in a poor lubrication effect, thereby accelerating the wear of internal components. Low temperature makes the oil viscous and has poor fluidity, which can easily cause poor oil circulation, resulting in insufficient pressure in the hydraulic cylinder and reduced load-bearing capacity. Abnormal fluctuations in oil temperature will have a long-term impact on the working performance of the hydraulic cylinder.
Aging and damage of seals: Seals are one of the key components of hydraulic cylinders. They are mainly responsible for sealing hydraulic oil, preventing leakage, and ensuring the pressure and stability of the hydraulic system. As the use time increases, the seals of the hydraulic cylinder will gradually age due to long-term pressure, temperature changes, and chemical reactions of the oil. When the seal is damaged, the sealing performance of the hydraulic cylinder deteriorates, resulting in pressure loss, which affects the load-bearing capacity. Especially in the case of damaged seals, leakage of hydraulic oil will lead to insufficient oil in the hydraulic cylinder, which will eventually lead to a decrease in load-bearing capacity.
Improper installation or non-standard use: Improper installation of the hydraulic cylinder or failure to comply with operating specifications during use will also lead to a decrease in its load-bearing capacity. For example, the hydraulic cylinder is not positioned strictly in accordance with the design requirements during installation, resulting in uneven force or deflection of the piston rod, which in turn leads to a decrease in the load-bearing capacity of the hydraulic cylinder. In addition, the operation of the hydraulic system also needs to strictly follow the relevant standards. Overload operation or non-compliance with regulations will burden the hydraulic cylinder and accelerate its performance degradation.
Design defects: Whether the design of the hydraulic cylinder is reasonable directly determines its service life and load-bearing capacity. If there are defects in the design of the hydraulic cylinder, such as the size of the piston and the piston rod not matching, or the layout of the oil circuit being unreasonable, the hydraulic cylinder will not be able to exert its due load-bearing capacity. Some design negligence may gradually appear after the hydraulic cylinder is put into use and eventually lead to a decrease in load-bearing capacity.
2. The impact of the decrease in the load-bearing capacity of the hydraulic cylinder
The decrease in the load-bearing capacity of the hydraulic cylinder will not only affect the operating efficiency of the equipment but may also bring a series of negative consequences:
Increased equipment failure rate: It will cause the load distribution of mechanical equipment to be uneven, resulting in frequent equipment failures and affecting production progress.
Reduced work efficiency: It will cause the equipment to work slower, or even fail to complete certain high-load operations, resulting in a decrease in overall work efficiency.
Increased energy consumption: The decrease in the load-bearing capacity of the hydraulic cylinder means that the hydraulic system requires higher pressure and more energy to maintain the same working effect, resulting in an increase in energy consumption.
Safety hazards: When the hydraulic cylinder cannot carry the normal workload, accidents such as equipment collapse and mechanical damage may occur, bringing serious safety hazards and even causing injuries to workers.
3. Measures to solve the decline in the bearing capacity of hydraulic cylinders
For various reasons for the decline in the bearing capacity of hydraulic cylinders, we can take the following measures:
Regular inspection and maintenance: In order to prevent the decline in the bearing capacity of hydraulic cylinders, regular inspection and maintenance are very necessary. Regularly check the wear of seals, piston rods, pistons, and other parts, and replace aging or damaged parts in time. In addition, check the quality of hydraulic oil to ensure that the oil is clean and meets the requirements.
Reasonable selection: The selection of hydraulic cylinders should be reasonably designed according to the actual working load and working conditions. If the working environment is more complex or the load is larger, a hydraulic cylinder with a higher bearing capacity can be selected to ensure its stable operation under extreme conditions.
Control load: During use, the working load must be strictly controlled to avoid long-term overload operation. Reasonable load distribution and appropriate working pressure can effectively reduce the risk of reduced bearing capacity of hydraulic cylinders.
Keep the oil clean: Keeping the hydraulic oil clean is the key to ensuring the bearing capacity of hydraulic cylinders. The oil should be replaced regularly and a suitable oil filter should be used to prevent contaminants from entering the hydraulic system. The water and impurities in the oil should be removed in time to avoid affecting the operation of the hydraulic cylinder.
Control the working temperature: The temperature of the hydraulic oil should be kept within an appropriate range. By installing a heat dissipation device and reasonably designing the oil circuit, the oil temperature can be effectively controlled to avoid the decrease in the hydraulic cylinder's load-bearing capacity due to abnormal temperature.
Optimize the design: In the design process of the hydraulic cylinder, the use environment and load conditions should be taken into consideration to ensure that the dimensions of each component match and to perform necessary strength checks. Reasonable design can effectively extend the service life and reduce the decrease in load-bearing capacity caused by improper design.
Use strictly in accordance with the operating specifications: The operator of the hydraulic system should strictly follow the operating specifications, not overload, not stop suddenly, and not start the hydraulic cylinder frequently. Reasonable operation can not only improve work efficiency but also effectively reduce the risk of decreased load-bearing capacity.
As the core component of the hydraulic system, the decrease in the load-bearing capacity of the hydraulic cylinder not only affects the operating efficiency of the equipment but may also bring a series of safety hazards and economic losses. Through regular maintenance, reasonable selection, keeping the oil clean, and controlling the load, the decrease in the hydraulic cylinder's load-bearing capacity can be effectively prevented, thereby ensuring the stable operation of the hydraulic system. In actual operation, users should take comprehensive preventive measures according to specific working conditions and needs to extend the service life of the hydraulic cylinder and improve its work efficiency.
www.toringcylinder.com
Ningbo Toring Machinery Manufacturing Co., Ltd.