Top Benefits of Powder Metallurgy in Modern Industry and Manufacturing
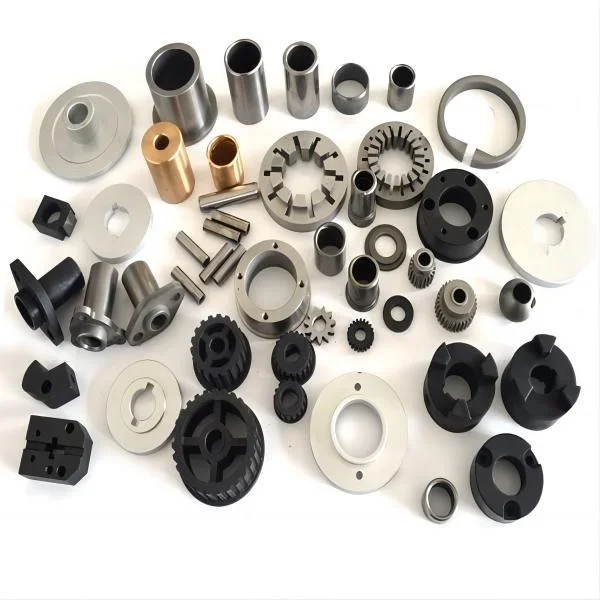
Powder metallurgy (PM) is an advanced manufacturing process that is increasingly revolutionizing industries by offering unparalleled benefits in the production of complex parts and materials. The process involves the production of metal powders, which are then compacted and sintered to form desired shapes. This innovative technology has paved the way for creating high-performance components across various sectors, including automotive, electronics, aerospace, and medical devices. In this blog post, we’ll explore the top benefits of powder metallurgy in modern industry and manufacturing, with insights from Ganlong-Flying, a company known for its expertise in precision turning, fasteners, screws, nuts, springs, stamping, and CNC machining, including powder metallurgy solutions.
1. Cost-Effective Production for Complex Parts
One of the primary advantages of powder metallurgy is its cost-efficiency, particularly for producing complex parts with intricate geometries that would be difficult or expensive to manufacture using traditional methods like casting or machining. The PM process allows manufacturers to create parts with minimal material waste, as the metal powders are precisely measured to form the desired shape without the need for extensive machining after sintering.
Ganlong-Flying leverages powder metallurgy to produce a wide range of high-precision parts used in industries such as IT, telecommunications, medical equipment, and automotive, ensuring cost-effective solutions for both small and large-scale production runs.
2. Improved Material Properties and Performance
Powder metallurgy offers the ability to create parts with superior material properties, such as increased strength, wear resistance, and thermal stability. The sintering process allows for precise control over the composition and microstructure of the material, which results in parts with better mechanical performance compared to those made from conventional manufacturing techniques.
For example, in applications involving high-stress environments such as motor components, electronic devices, and machinery, powder metallurgy can be used to produce parts that are both durable and resistant to wear. At Ganlong-Flying, their expertise in precision powder metallurgy ensures the production of high-performance components for critical applications in industries like medical devices, scientific instruments, and automotive systems.
3. High Precision and Consistency
Powder metallurgy allows for the production of parts with high dimensional accuracy and consistency. Once the metal powders are compacted into molds, the sintering process solidifies them into a precise shape, reducing the need for further machining. This is especially important for industries that require tight tolerances and high-quality standards.
Ganlong-Flying’s advanced manufacturing capabilities include CNC precision processing, which complements powder metallurgy by enabling the creation of custom-designed parts with precise dimensions. This capability is especially beneficial for industries such as medical equipment, where component accuracy can be critical for proper function and safety.
4. Sustainable and Environmentally Friendly Manufacturing
Powder metallurgy is an environmentally friendly manufacturing process that produces minimal waste compared to traditional machining methods. Because the metal powder is precisely metered and compacted into the final shape, there is little to no excess material that would otherwise go to waste. Additionally, the sintering process typically requires less energy than casting or forging methods, making it a more sustainable option.
Ganlong-Flying’s commitment to sustainable practices aligns with the growing demand for eco-friendly manufacturing solutions. Their use of powder metallurgy contributes to reducing material waste and energy consumption while maintaining the high quality and performance of the components they produce.
5. Flexibility in Material Selection
Powder metallurgy provides manufacturers with a wide range of material options, including metals, alloys, and composite materials. This flexibility allows for the creation of parts that are optimized for specific applications, whether it’s a lightweight material for aerospace or a corrosion-resistant alloy for medical devices.
Ganlong-Flying’s ability to work with various materials, including high-performance alloys and custom formulations, ensures that their powder metallurgy solutions can meet the specific requirements of industries such as telecommunications, automotive, and electronics. The versatility of this process allows them to create components that can withstand extreme conditions, whether in high-temperature environments or highly corrosive settings.
6. Reduced Labor and Tooling Costs
Since powder metallurgy involves minimal post-processing and does not require extensive machining or secondary operations, it reduces labor and tooling costs. The precision of the PM process also reduces the need for costly adjustments during production, making it an ideal choice for mass production runs of small, intricate parts.
Ganlong-Flying’s use of advanced powder metallurgy, coupled with their extensive experience in CNC precision machining, helps customers achieve cost-efficient production without compromising on quality. This enables businesses to meet market demands quickly while keeping costs manageable.
7. Wide Range of Applications
Powder metallurgy is widely used across various industries, including IT, medical devices, automotive, electronics, and more. Components such as gears, bearings, bushings, filters, and electrical contacts are commonly produced using PM. The ability to create highly specialized components means that powder metallurgy can address the unique demands of these diverse sectors.
At Ganlong-Flying, powder metallurgy is used to manufacture components for a wide variety of industries, from smartphone and server parts to automotive and medical device components. Their expertise ensures that each product is tailored to meet industry-specific requirements for performance, reliability, and cost-effectiveness.
Conclusion: The Future of Manufacturing with Powder Metallurgy
Powder metallurgy is increasingly becoming a preferred manufacturing method in modern industries due to its numerous advantages, including cost efficiency, material performance, precision, and sustainability. With the ability to produce complex parts with minimal waste and high consistency, powder metallurgy is set to play a significant role in advancing technology and meeting the demands of various industries.
Ganlong-Flying, with its extensive experience in powder metallurgy, is committed to providing innovative solutions that help businesses optimize their production processes and achieve superior results. Whether you need high-precision automotive components, durable medical device parts, or custom-designed products for the telecommunications industry, powder metallurgy offers the ideal solution for modern manufacturing challenges.
If you're looking for advanced, high-quality components, Ganlong-Flying’s expertise in powder metallurgy and precision machining ensures that your production needs are met with excellence and efficiency.
www.ganlongflying.com
Dongguan City Ganlong-Flying Industrial Corporation Limited