Manufacturing process of double channel heat exchanger
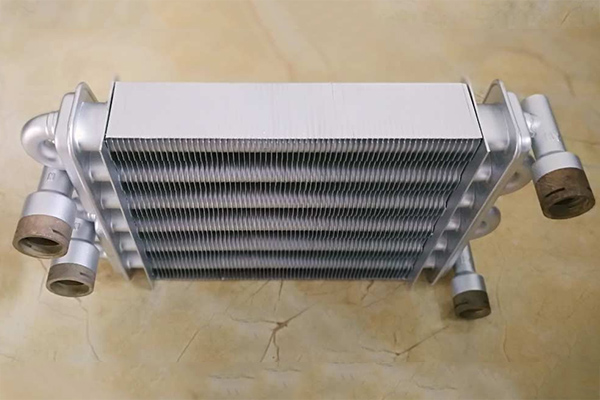
In the realm of heating solutions, the efficiency and reliability of heat exchangers are paramount. Double channel heat exchangers, with their unique design, have become increasingly popular for their ability to optimize heat transfer. Sichuan ISAAC International Trading Co., Ltd., a leading manufacturer and supplier of heating systems, has been at the forefront of producing high-quality double channel heat exchangers. This article delves into the manufacturing process of these essential components, highlighting the meticulous steps that go into creating six-tube double channel heat exchangers and other variants.
Understanding Double Channel Heat Exchangers
Double channel heat exchangers are engineered to maximize the surface area for heat transfer, thereby enhancing efficiency. These heat exchangers are designed with two channels through which fluids flow, allowing for effective heat exchange between the two streams. The six-tube double channel heat exchangers, in particular, are known for their compact design and high performance.
The Manufacturing Process
-
Design and Planning: The manufacturing process begins with the design and planning stage. Engineers at ISAAC utilize advanced CAD software to design the heat exchangers, ensuring that they meet the required specifications and performance standards.
-
Selection of Materials: The choice of material is crucial for the heat exchanger's durability and heat transfer capabilities. Typically, materials such as copper, stainless steel, or aluminum are used due to their thermal conductivity and resistance to corrosion.
-
Tube Formation: In the case of six-tube double channel heat exchangers, the tubes are formed using extrusion or drawing processes. These tubes are then subjected to rigorous quality control checks to ensure they meet the required dimensions and tolerances.
-
Header Assembly: The headers are the end pieces that connect the tubes and direct the flow of fluids. They are precision machined to ensure a perfect fit and are designed to withstand the pressure of the fluids flowing through the heat exchanger.
-
Welding: The tubes are then welded to the headers. This process requires skilled welders and advanced equipment to ensure a strong and leak-proof joint. The welds are inspected using non-destructive testing methods to guarantee their integrity.
-
Cleaning and Passivation: After welding, the heat exchangers are cleaned to remove any debris or contaminants. Passivation, a process that involves treating the surface with a chemical solution, is performed to create a protective oxide layer on the metal, enhancing its resistance to corrosion.
-
Pressure Testing: Each double channel heat exchanger undergoes rigorous pressure testing to ensure it can handle the operational pressures without failure. This step is crucial for ensuring the safety and reliability of the heat exchanger in real-world applications.
-
Quality Inspection: Before being packaged and shipped, the heat exchangers are subjected to a final quality inspection. This includes visual inspections, dimensional checks, and performance testing to ensure they meet ISAAC's high standards.
-
Packaging and Shipping: The double channel heat exchangers are carefully packaged to protect them during transit. ISAAC ensures that each unit is securely packed to prevent damage and is ready for installation upon arrival.
Advantages of Double Channel Heat Exchangers
-
Efficiency: The double channel design allows for a larger surface area for heat transfer, resulting in higher efficiency compared to single channel designs.
-
Compactness: These heat exchangers are designed to be compact, making them ideal for applications where space is limited.
-
Versatility: They can be used in a wide range of applications, from residential heating systems to industrial processes, making them a versatile choice.
-
Reliability: The manufacturing process ensures that each unit is built to last, with attention to detail and quality control at every step.
The Role of ISAAC in the Industry
Sichuan ISAAC International Trading Co., Ltd. plays a significant role in the industry by providing high-quality double channel heat exchangers for sale. Their commitment to excellence in manufacturing and customer service has made them a trusted partner for businesses and consumers alike.
Conclusion
The manufacturing process of double channel heat exchangers is a testament to the precision and expertise required in the heating industry. With companies like ISAAC leading the way, the future of heating solutions is in capable hands. As the demand for efficient and reliable heat exchangers grows, the six-tube double channel heat exchangers and other variants will continue to play a crucial role in meeting these needs.
About Sichuan ISAAC International Trading Co., Ltd.
Sichuan ISAAC International Trading Co., Ltd. is a renowned manufacturer and supplier of heating systems, including a wide range of double channel heat exchangers. With a focus on quality, innovation, and customer satisfaction, ISAAC continues to set the standard for excellence in the industry.
www.isaacoutlets.com
ISAAC