How Does DTF Printer Work
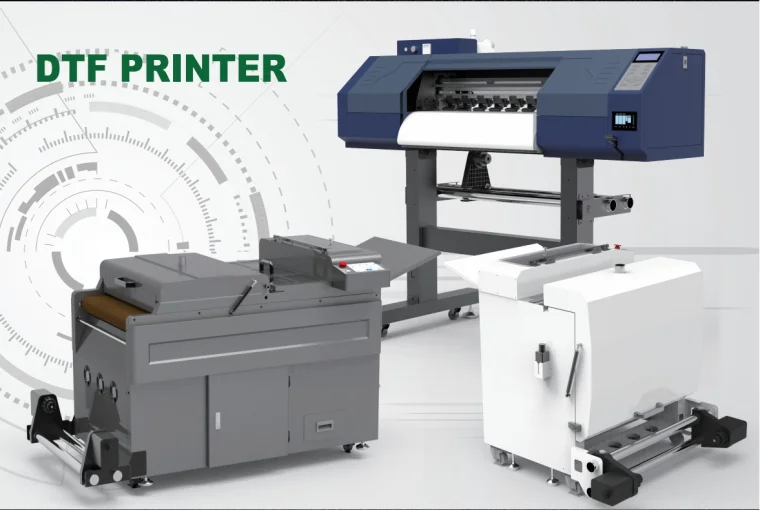
Direct to Film (DTF) printing is a revolutionary technology that has transformed the world of garment decoration and textile printing. DTF printers offer a cost-effective and efficient solution for producing vibrant, high-quality prints on various fabrics. In this article, we will delve into the working mechanism of DTF printers, exploring the process step by step. Let's unlock the secrets behind this innovative printing technology and understand how it has revolutionized the textile industry.
I. Understanding DTF Printing
A. What is DTF Printing?
DTF printing, also known as Direct to Film printing, is a digital printing technique that enables the direct transfer of designs onto fabric using specialized ink and heat. Unlike traditional printing methods, DTF printing eliminates the need for intermediate steps such as screen printing or heat transfers, resulting in faster production and greater design flexibility.
B. Advantages of DTF Printing:
DTF printing offers numerous advantages over traditional printing methods, including vibrant and long-lasting prints, high resolution, versatility in fabric selection, and the ability to print complex designs with intricate details. It also allows for cost-effective production, as it eliminates the need for screen preparation and reduces ink wastage.
II. The Working Mechanism of DTF Printers
A. Preparing the Design:
The first step in DTF printing is designing or selecting the artwork to be printed. This can be done using graphic design software or by choosing pre-made designs. Once the design is ready, it is sent to the DTF printer for processing.
B. Coating the Film:
A special film coated with a white adhesive layer is used in DTF printing. The film is loaded onto the printer and passes through a roller system, where a thin layer of adhesive is applied to the surface of the film. This adhesive layer ensures proper adhesion of the ink to the fabric during the transfer process.
C. Printing the Design:
The coated film is then fed into theDTF printer, where the design is digitally printed onto the adhesive layer using specialized DTF inks. The printer uses advanced inkjet technology to precisely deposit the ink onto the film, resulting in vibrant colors and sharp details.
D. Curing the Ink:
After the design is printed, the ink needs to be cured or dried before it can be transferred to the fabric. This is typically done using a heat press or a specialized curing unit. The heat and pressure applied during the curing process ensure that the ink adheres firmly to the adhesive layer, ready for transfer.
E. Transferring the Design:
Once the ink is cured, the film with the printed design is ready for transfer onto the fabric. The film is placed on top of the fabric, with the printed side facing down. Heat and pressure are applied using a heat press, which activates the adhesive layer, causing it to bond with the fabric. The heat also helps the ink to penetrate the fibers of the fabric, resulting in a durable and long-lasting print.
F. Peeling and Finishing:
After the transfer process is complete, the film is carefully peeled off, leaving behind the vibrant and fully transferred design on the fabric. Depending on the type of fabric and design, additional finishing steps such as washing or curing may be required to enhance the durability and colorfastness of the print.
III. Maintenance and Tips for DTF Printers
A. Printer Maintenance:
To ensure optimal performance and longevity of the DTF printer, regular maintenance is crucial. This includes cleaning the print heads, checking ink levels, and calibrating the printer as needed. Following the manufacturer's guidelines for maintenance and cleaning procedures is essential.
B. Choosing the Right Fabrics:
DTF printing is compatible with a wide range of fabrics, including cotton, polyester, blends, and even non-textile materials such as leather or wood. However, it is important to select fabrics that are suitable for the DTF process and can withstand the heat and pressure applied during transfer.
C. Design Considerations:
When preparing designs for DTF printing, it is important to consider factors such as resolution, color saturation, and complexity. Higher resolution designs and vibrant colors tend to yield better results. Additionally, intricate details and fine lines may require special attention during printing to ensure accurate reproduction.
Conclusion
In conclusion, DTF printers offer a versatile and efficient printing solution to the printing industry. By understanding how DTF printers work and the processes involved, businesses can take advantage of this innovative technology. With their vibrant colors, durability, and cost-effectiveness, DTF printers open up new possibilities for creative expression and business growth. Whether you are in the fashion industry, promotional products business, or just want to add a unique touch to your designs, DTF printers can be used for you.
DTF Printer: A New Choice For Efficient And Environmentally Friendly Clothing Printing
Orinjet Digital Technology
LornaChia@orinjet.com