How Upgrading Your Plastic Extruder Auxiliary Parts Can Boost Production Performance
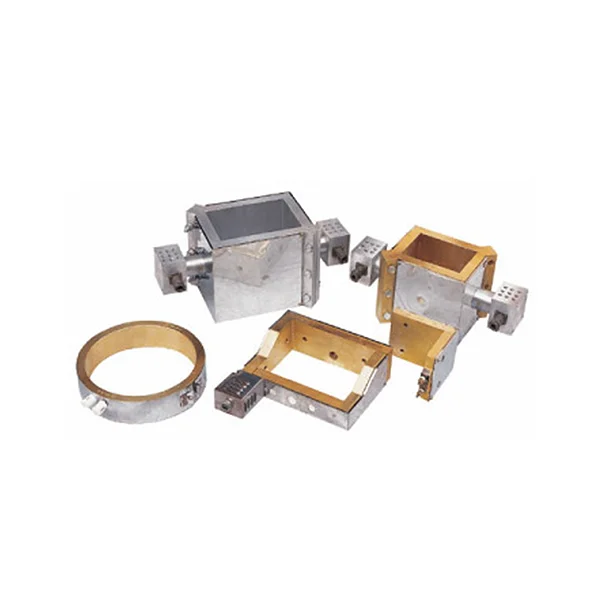
In the fast-evolving plastic industry, keeping pace with the latest technological advancements is key to staying competitive. One such opportunity for improvement lies in upgrading the auxiliary parts of your plastic extruder. While the extruder itself plays a vital role in the production process, it’s often the auxiliary equipment that can significantly enhance overall performance, increase efficiency, and reduce downtime.
What Are Plastic Extruder Auxiliary Parts?
Plastic extruders are complex systems that process raw plastic materials into finished products through heat and pressure. However, a lot of the success of an extrusion process hinges on the effectiveness of the auxiliary components. These auxiliary parts include a variety of components like feeders, cutters, die heads, screens, cooling systems, and downstream equipment. When these parts work seamlessly together, the entire production process is smoother, more efficient, and cost-effective.
Why Upgrade Auxiliary Parts?
-
Increased Efficiency and Speed
Upgrading your extruder’s auxiliary parts can enhance the throughput of your production line. For example, more advanced feeding systems can ensure better material consistency, which reduces the chances of defects or delays in production. Additionally, more efficient cooling systems can increase processing speeds, allowing for faster turnaround times and higher output. -
Enhanced Product Quality
The precision of auxiliary equipment plays a huge role in determining the quality of the final product. By upgrading parts like die heads or screen changers, you can achieve more uniform material distribution and smoother surface finishes. For companies like JiaXin Mechanical Manufacture, which specializes in extrusion lines for composite and recycling processes, product quality is paramount, and an upgrade to auxiliary systems can directly enhance performance in this area. -
Cost Savings
While upgrades involve initial investment, they often lead to long-term savings. Improved auxiliary parts reduce wear and tear on your primary extruder, prolonging the life of the machine and lowering maintenance costs. Furthermore, optimized systems tend to use less energy and require fewer resources, which directly impacts the bottom line. -
Increased Flexibility and Versatility
Upgrading auxiliary parts allows for greater flexibility in production. Newer systems offer more control over temperature, pressure, and material feeding, which is particularly important in industries like composite and recycling, where different materials and processes need to be handled. JiaXin Mechanical Manufacture’s advanced solutions for multi-functional processes such as PET recycling production lines and composite extrusions benefit greatly from these upgrades, allowing operators to fine-tune processes to achieve the best results for a variety of applications. -
Reduced Downtime and Maintenance
Upgrades can also reduce downtime caused by mechanical failure. More durable and efficient auxiliary parts result in fewer breakdowns and less maintenance, allowing operators to focus on production rather than troubleshooting. The improved reliability of these components leads to fewer interruptions, ensuring that your production line operates smoothly and consistently.
JiaXin Mechanical Manufacture: Driving Innovation in the Plastic Extrusion Industry
JiaXin Mechanical Manufacture is at the forefront of designing and manufacturing advanced extrusion systems. Their focus on composite and recycling process lines, including twin-screw extruders, single-screw extruders, sheet production lines, and PET recycling lines, makes them an industry leader. By continually integrating new technologies and improving the efficiency of auxiliary equipment, JiaXin ensures that its clients can achieve optimal performance in all phases of the production process.
The company’s commitment to providing turnkey solutions means that when customers invest in new auxiliary parts or upgraded systems, they receive the best possible integration into their existing processes. This approach is crucial for industries that require precision and versatility, such as in the production of composite materials or in recycling operations where consistent quality and efficient resource use are vital.
Conclusion
Upgrading the auxiliary parts of your plastic extruder can provide significant benefits that go beyond just improved efficiency. By enhancing product quality, reducing downtime, and cutting long-term costs, manufacturers can see a clear return on investment. As the industry continues to advance, companies like JiaXin Mechanical Manufacture are providing the expertise and advanced solutions needed to stay ahead in this competitive market. By investing in the latest technologies and continually improving auxiliary systems, plastic extrusion manufacturers can boost their production performance and pave the way for greater success in the years to come.
www.tcextruder.com
JiaXin Mechanical Manufacture CO., Ltd