Exploring the Various Types of Material Requirements Planning
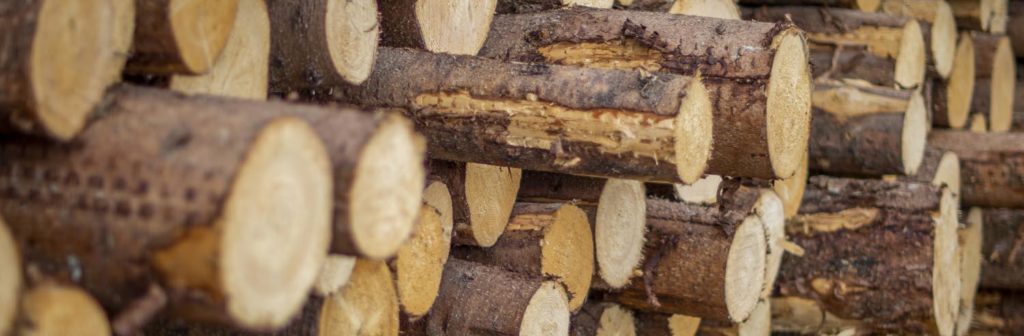
Material Requirements Planning (MRP) is a crucial process in supply chain management that helps organizations effectively manage their inventory and production schedules. By analyzing demand, inventory levels, and lead times, MRP enables businesses to optimize their material flow and ensure timely production. In this article, we will delve into the different types of Material Requirements Planning and explore their unique features and applications.
- Traditional Material Requirements Planning (MRP):
Traditional MRP is the foundational approach to managing material requirements. It involves analyzing demand, calculating net requirements, and generating purchase orders or production orders accordingly. This type of MRP is suitable for businesses with stable demand patterns and predictable lead times. - Distribution Requirements Planning (DRP):
DRP extends the scope of MRP to include the management of finished goods inventory across multiple distribution centers or warehouses. By considering factors such as transportation costs, lead times, and customer demand, DRP helps organizations optimize their distribution network and ensure product availability at the right locations. - Manufacturing Resource Planning (MRP II):
MRP II takes MRP to the next level by integrating it with other business functions such as finance, human resources, and capacity planning. This comprehensive approach enables organizations to align their material requirements with overall business objectives, optimize resource utilization, and improve decision-making across different departments. - Just-in-Time (JIT):
JIT is a lean manufacturing approach that aims to minimize inventory levels by synchronizing material flow with production schedules. Unlike traditional MRP, JIT focuses on reducing waste, lead times, and carrying costs. By adopting JIT principles, businesses can achieve greater efficiency, cost savings, and improved customer satisfaction. - Advanced Planning and Scheduling (APS):
APS systems combine MRP with advanced algorithms and optimization techniques to create detailed production schedules. These systems consider various constraints such as machine capacities, labor availability, and material availability to generate feasible and optimized production plans. APS helps organizations achieve higher productivity, reduce bottlenecks, and respond quickly to changing customer demands.
Conclusion:
Material Requirements Planning plays a vital role in managing inventory and production processes effectively. By understanding the different types of MRP, businesses can choose the most suitable approach based on their specific requirements and industry dynamics. Whether it's traditional MRP, DRP, MRP II, JIT, or APS, each type offers unique benefits and applications. By leveraging the right MRP strategy, organizations can streamline their operations, reduce costs, and gain a competitive edge in the market.