How Does Vacuum Extruder Work in Clay Brick Production
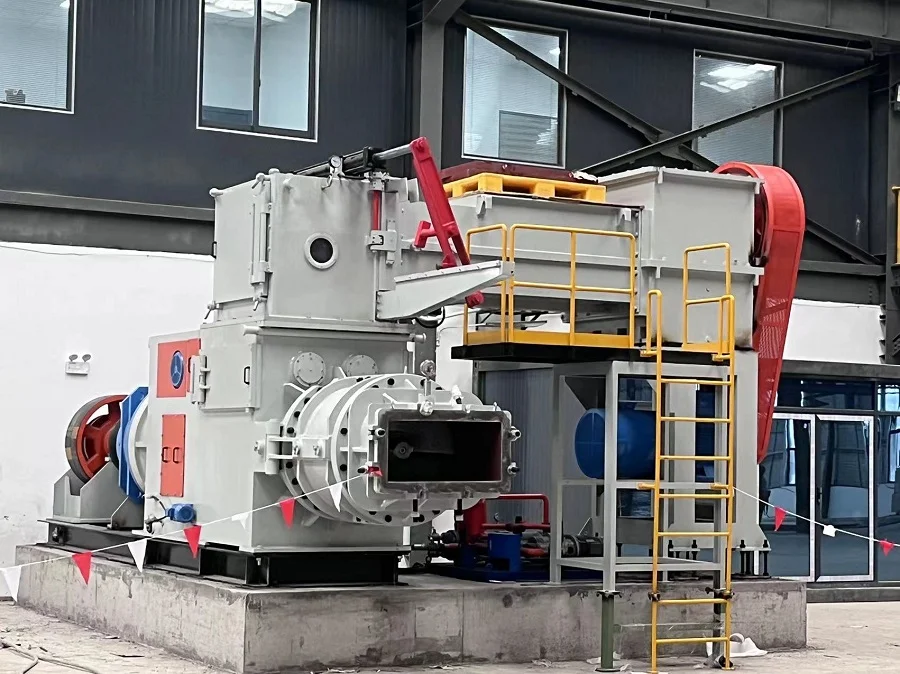
In the world of brick manufacturing, vacuum extruders play a vital role in producing high-quality clay bricks efficiently. These machines utilize a unique process that involves the extrusion of clay through a vacuum chamber. In this article, we will explore the working principles of a vacuum extruder and shed light on the various stages involved in clay brick production using this technology.
I. Understanding Vacuum Extruders
Overview of Vacuum Extruders:
A vacuum extruder is a specialized machine used in the production of clay bricks. It combines the processes of clay preparation, molding, and drying, resulting in the creation of durable and uniform bricks.
Key Components of a Vacuum Extruder:
A vacuum extruder consists of essential components, including a clay hopper, an auger or screw, a vacuum chamber, and a die. These components work together to facilitate the extrusion and shaping of clay into bricks.
II. The Working Process of a Vacuum Extruder in Clay Brick Production
Clay Preparation:
The first stage involves the preparation of clay. The raw clay is sourced, then passed through a series of processes such as crushing, mixing, and refining to achieve the desired consistency and remove any impurities.
Clay Feeding:
The prepared clay is then loaded into the clay hopper of the vacuum extruder. The hopper feeds the clay into the machine, where it is gradually moved forward by an auger or screw.
Extrusion:
As the clay moves forward, it encounters increasing pressure from the rotation of the auger or screw. This pressure forces the clay through a shaped die, resulting in the extrusion of a continuous column of clay known as a "slug."
Vacuum Chamber:
Once the slug of clay is extruded, it enters a vacuum chamber. The vacuum chamber is designed to remove any air trapped within the clay, ensuring better compaction and eliminating the risk of air pockets within the bricks. The vacuum also helps in enhancing the brick's density and strength.
Cutting and Shaping:
After the vacuum process, the extruded clay slug is cut into individual brick-sized pieces. These pieces are then shaped according to the desired brick dimensions using a cutting mechanism or wire cutter. The excess clay is removed, and the shaped bricks are ready for the drying stage.
Drying:
The freshly shaped clay bricks are placed on drying racks or conveyors and subjected to a controlled drying process. This allows the bricks to lose moisture gradually, resulting in reduced shrinkage, improved strength, and minimized cracking.
Firing:
Once the drying process is complete, the bricks are fired in a kiln to achieve the final hardness and durability. The firing temperature and duration depend on the type of clay used and the desired properties of the bricks.
III. Advantages of Using a Vacuum Extruder in Clay Brick Production
Improved Quality:
The vacuum extrusion process ensures uniform density and reduced porosity in the clay bricks, resulting in enhanced strength and durability.
Increased Production Efficiency:
Vacuum extruders offer high production rates, allowing for faster clay brick production compared to traditional methods. The continuous extrusion process minimizes downtime and optimizes workflow.
Energy Efficiency:
The vacuum process eliminates the need for excessive water use during shaping, reducing energy requirements for drying and firing.
Cost Savings:
Efficient production, reduced energy consumption, and improved brick quality contribute to cost savings in the long run.
IV. Maintenance and Care for Vacuum Extruders
Regular Cleaning:
Clean the machine regularly to remove any clay residue that may accumulate in the hopper, auger, and vacuum chamber. This helps maintain optimal performance and prevents blockages.
Lubrication:
Ensure that all moving parts are properly lubricated to minimize friction and extend the machine's lifespan.
Routine Inspections:
Regularly inspect the machine for any signs of wear, damage, or misalignment. Address any issues promptly to avoid further complications.
V. Conclusion
Vacuum extruders have revolutionized the clay brick production process, offering improved quality, increased efficiency, and cost savings. By understanding the working principles behind these machines and following proper maintenance practices, manufacturers can optimize their clay brick production and deliver superior products to the market. Incorporating vacuum extrusion technology in brick manufacturing is not only beneficial for businesses but also contributes to sustainable and durable construction practices.
At KeLi Machine, we specialize in providing high-quality vacuum extruders for clay brick production. Our machines are designed to meet the specific needs of the industry, ensuring efficient and reliable operations. Contact us today to learn more about our vacuum extruders and how they can enhance your brick manufacturing process.
Explore The Advantages of KeLi Machine Vacuum Extruder in Cement Brick Production
KeLi Machine
13961552599@163.com